Wood Manufacturing
Metalwood bodies are predominantly either investment cast or stamped construction. Golfers may refer to the wood as being 'forged' however few woods have parts to them forged other than the face. While nearly all of today's modern drivers are made out of titanium it is possible to find older stainless steel drivers in addition to inexpensive aluminum ones. For fairway and hybrid woods stainless steel is the material of preference. While the billet forging and investment casting pages on this site show the processes in detail, below are some aspects to metalwood construction that make their construction unique.
Stamped Wood Construction

A stamping machine is very similar to a forging press. A tremendous amount of force is used to create the part using dies of the appropriate shape. Forging presses will form a shape from a billet while the stamping presses cut it from a sheet.
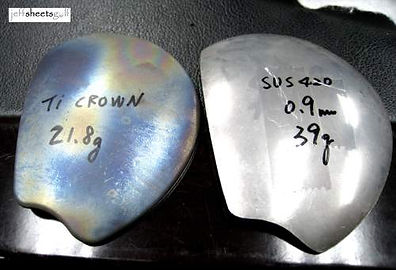
After the shape is stamped from the sheet metal it is stamped again in a die that has the appropriate radius form to it. The two pieces above began as flat sheet metal and following the second stamping are shaped as crowns.

Above is a sole stamping that also incorporates two weighting ports. These too are stamped in subsequent operations.
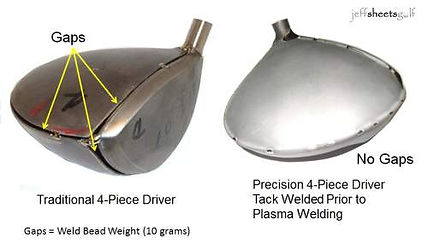
Above left is a traditional stamped driver. It is TIG welded together where welding rod is used to apply a bead to fill in the gaps between the parts. A precision stamping requires no weld rod to join the parts together (saving on weight).

Above is a strip of beta titanium in which driver faces have been stamped from. Alongside are maraging steel sheets that were used to stamp out high strength steel iron faces.
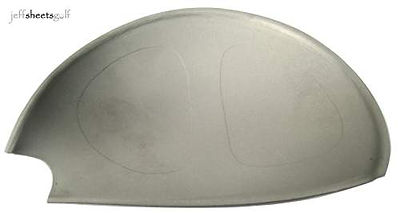
Higher pressure stamping machines can add further detail to the part. This is the interior of a titanium driver crown that has two thinner sections within it.

Some of the more sophisticated stampings can be extremely precise in their geometry. Above is a tongue and grooved face that interlocks with the sole (and crown too, not shown).

Precision stampings incorporate juncture lips that melt together in a plasma welding process. Unlike a traditional stamping which gets heavier once it is welded and polished, the precision stamping results in a lighter part after is polishing operation.
Investment Cast Woods

The tooling for an investment cast wood can be very complex. Unlike a stamped wood which produces separate crown, sole and face pieces, investment cast tooling will produce the bulk of the head. Most titanium drivers use a face-pull design meaning that the entire head is cast without the face. A complex puzzle piece acts as the interior core to the wood enabling it to be hollow. The core is broken down like a 3D puzzle and extracted through the face opening of the driver.
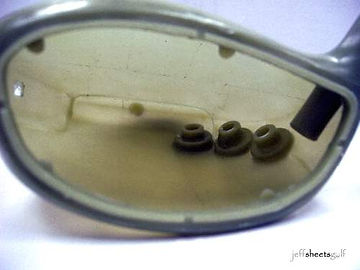
Pictured here is a titanium driver design with a face-pull construction in wax form. Notice how thin the wax walls are - light permeates through them for this thin walled construction.

Fairway wood waxes are assembled to a wax tree. This design has the face cast into the head and uses a separate crown piece to be welded to complete the design.

This is a titanium furnace which is much larger than stainless steel furnaces. It consumes a tremendous amount of energy. These are often run at night time when energy demand is lower.

Investment cast 3-woods with face pull construction. Ready for face inserts to be welded.
Billet Forged Wood Faces

Forging dies for a billet forged face design. This is for a variable face thickness (see ellipse in center of face at left) and also a cup face design (see lip around face on right). If you go to the expense of a billet forged face it should at least incorporate variable face thickness to its design.

Billet forged cup face coming off of the forging press. The material is still very hot even though it is no longer cherry red.
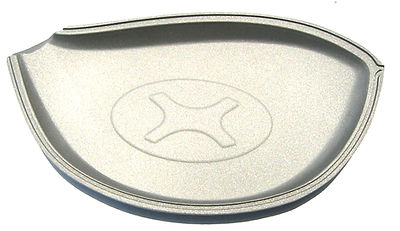
Here is a precision forged cup face design with an CNC milled groove around the face for tongue and groove construction.

Here is a simple forged face, no cup design, being plasma welded into an investment cast head. The lip around the face opening is melted onto the forged face insert with precision isolated heat.
Additional Wood Processes

Many of today's woods incorporate a dark metal finish to them. This is known as a PVD (physical vapor deposition) coating. The PVD can be applied in a variety of colors however black and dark gray are most popular with manufactures. The PVD coating is applied in a vacuum chamber as shown above.

X-Ray is used to check the porosity in metalwood heads so that pin holes can be repaired prior to the head being finished. This minimizes bad parts making it into the hands of golfers.



Metal analyzers are used to record production results of club heads. Swatch samples are retained along with metallurgy reports for customer reference.