
Not every prototype model developed makes it to a production launch. While just as many (if not more) hours are spent on the engineering and testing of clubs that don’t make it to market, often the reason they’re not introduced is just a matter of circumstance. The following clubs never made it to market for one reason or another. Sometimes it was performance-related while other times the sound or manufacturing process became too much of a challenge. In any case each of these models were either Doomed (by the marketing department) or declared Duds.

Brand: Snake Eyes
Model: Brass Body Wedges
Material/Mfg: Soft 304 Stainless Steel Frame and Hosel with Brass Body
Conventional wisdom would presume that this model would result in a soft feeling wedge. There have been a number of brass insert wedges produced in the past but this design takes the construction a step further by incorporating brass as the primary body material held within a steel frame. Unfortunately the two soft materials it was produce from, 304 stainless steel and solid brass, together made a harsh feeling golf club. It likely could have been the construction method however I have produced many titanium face irons in a similar fashion that have felt quite good. Little effort was spent trying to improve this particular design due to the number of other Snake Eyes wedges I had under development at the same time.
Fate: Dud

Brand: Golfsmith
Model: Attack Irons
Material/Mfg: Investment Cast 431 Stainless Steel
The design concept of the Attack iron involved a very thin face in the upper section of the score line area. This allowed a good amount of weight displacement which went into the flying buttress feature. The buttress joined the back side of the face with a pressure fit urethane dampening device that helped channel impact vibrations into the flying buttress. While this system proved to worked as intended the U.S.G.A. wasn’t a fan of the design. The flying buttress made the iron non-conforming to the Rules of Golf. If a string can be passed into one opening and exit out another the U.S.G.A. will likely deem it non-conforming. They chose to do that in the case of the Golfsmith Attack irons. Recently the U.S.G.A. changed their position on the string rule.
Fate: Dud

Brand: Golfsmith
Model: MX3 Transitional Set
Material/Mfg: Investment Cast 431 Stainless Steel with Urethane Dampner
I really liked this set of irons but the plans of launching of them died just as the first prototypes were completed. They were a product line extension of the highly customizable MX3 woods, irons and putters. The decision to discontinue the MX3 family led to the ultimate demise of this design. The urethane inserts ranged from 4 – 30 grams while retaining identical dimensions to one another making them interchangeable between the irons, woods, wedges and putters.
Fate: Doomed

Brand: Golfsmith
Model: Twin Tune Transitional Irons
Material/Mfg: Investment Cast 431 Stainless Steel with Adjustable Weights
Once the MX3 transitional set irons were discontinued I furthered the design concept using two screw ports for greater weight adjustability. This resulted in greater flexibility of changing weights without the mess of epoxying the urethane inserts in place. Each screw port accommodated screws ranging from 2 – 8 grams depending on which material they were constructed from (aluminum, steel and tungsten). This turned into one of those “lost” projects where it somehow never made it into production. At the time of their development we were launching 65 unique models per year for Golfsmith. This was one of the many uncounted models that were never sold.
Fate: Doomed

Brand: A.S.I.
Model: Franklin Irons
Material/Mfg: Investment Cast 431 Stainless Steel with Adjustable Weights
The AIS Franklin irons were one of those design abominations that I’m frankly quite happy never made it to market. The challenge was to create an iron that had a great latitude of bias and weight adjustment. Using five weight ports the Franklin iron was capable of accepting plastic, aluminum, steel, brass and tungsten set screws. The different set screw materials each had their own unique density to them and the club fitter could mix and match the different material types to achieve the desired weight distribution. While the medallion was never developed to finish off the Franklin’s cosmetic look it would not have been able to overcome the Frankenstein-ish appearance of the irons.
Fate: Doomed

Brand: A.S.I.
Model: No-Name Game Improvement Irons
Material/Mfg: Investment Cast 431 Stainless Steel
This no-name A.S.I. iron utilized two screw ports to allow weight and bias adjustability in its wide sole oversize design. Intended as a maximum game improvement club for Golfsmith’s Elite Clubmaker Program a change in foundries led to a different model that incorporated a hosel weight port behind the face (A.S.I. Edison). As with the ASI Franklin iron, this model looked more utilitarian than graceful. While it had a high moment of inertia and got the ball airborne easily I was never a big fan of its appearance. The creation of the deep screw ports towards the heel and toe made this design very awkward. Shifting them towards the center of the club would have enabled me to trim the sole width down but they were functionally more effective (for MOI) in the heel and toe. Even though you can create a highly functional design, if the elegance of it is lacking then it’s time to go back to the drawing board and begin again. That we did.
Fate: Doomed
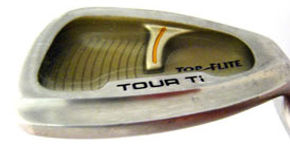
Brand: Spalding Top-Flite
Model: Tour Ti Irons with Solid Cavities
Material/Mfg: Investment Cast 17-4 Stainless Steel Body with Titanium Face and Urethane Cavity
I had created a number of urethane-filled cavities in the Top-Flite Tour irons using varying amounts of material in each cavity. The 100% filled cavity was the prototype of choice to our tour staff. The first full set of these I created also had the first prototype Muscle shafts in them. Lee Trevino took that set and won the Legends of Golf tournament. The Monday after his victory I was reading Lee’s quotes about the urethane filled cavities that Top-Flite would one day be coming out with. Unfortunately we never got the foundries in Asia to work efficiently with the material and the urethane filled cavities never went to market. But boy did they feel sweet!
Fate: Doomed


Brand: Wilson Golf
Model: Direct Connect Putters
Material/Mfg: Milled Aluminum and Stainless Body, Aluminum Shaft, Dual Durometer Grips
The Direct Connect concept incorporated the same material (aluminum) running from the impact area (face) up the shaft to the hands for distinctive feel and feedback while putting. A heavier steel frame encased the aluminum center of the putter providing the necessary static weight and higher moment of inertia. Using aluminum for the putter shaft provided a different feel compared to a steel face and steel shaft combination. To further enhance impact feedback the putter grip utilized a patented thin front panel which was produced in a clear urethane. A variety of putter head models were developed but the project never went to market following prototyping. All samples had been 100% CNC milled in the U.S. which was not very cost effective from a production standpoint. However we never received the green light to move the program into production.
Fate: Doomed

Brand: Lynx
Model: LX Tour DC
Material/Mfg: Billet Forged 1035 Carbon Steel with 100% CNC Milled Cavity
In 2009 the Lynx LX Tour MC irons were introduced and they were originally going to be accompanied with a wider sole, larger face Tour DC sibling. Just like the Tour MC irons, the Tour DC were billet forged and the cavity 100% CNC milled to final dimensions. This model was a successor to the Lynx Black Cat Tour DC forgings which were a popular model for Golfsmith Elite Clubmakers. The LX Tour DC was a much improved face profile over its predecessor but that alone was not enough to get Golfsmith to commit it to the product line as a completely assembled set. The Elite program was disbanded and along with it a high quality game improvement forging in the Tour DC.
Fate: Doomed

Brand: Lynx
Model: Black Cat MC Irons
Material/Mfg: Billet Forged 1030 Carbon Steel
After the success of the Black Cat Tour MC/DC irons this new Black Cat MC design was created by my assistant David Cersley. Unlike its predecessor it was billet forged to shape as opposed to being forged and then having the cavity CNC milled. The decision to move this iron forward as a complete club instead of a component in Golfsmith’s Elite Clubmakers Program caused the marketing team to rethink its launch. My R&D staff was asked to convert the forged tooling dies from this design into an oversized thick blade so that blank forgings had the flexibility of being 100% CNC milled for a multitude of different designs from the same tooling. Cersley has played with this prototype since measuring the first test samples and refuses to consider any other iron design for his own bag.
Fate: Doomed
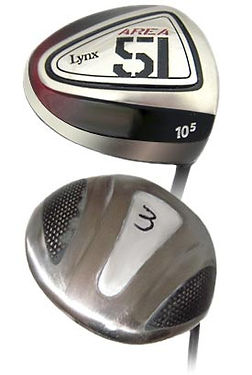
Brand: Lynx
Model: Area 51
Material/Mfg: Investment Cast 6-4 Titanium and 15-3-3-3 Beta Titanium Face
Boy, if I could add up the number of hours we had spent on this project it would be scary to see the total number of hours trying to make this driver sound acceptable. The Area 51 pushed all of the U.S.G.A. maximum dimensions for face length, breadth, height and volume. I cannot say that all of the hours we spent on this project were wasted, because they weren’t. We learned quite a lot about sound tuning, body deflection and internal reinforcement structure. From the very first prototypes which incorporated carbon fiber sole windows and an aluminum composite sole plate, the Area 51 was an outstanding performer. As the design evolved into its final 100% titanium configuration we continued to see improvements in performance but didn’t have enough ear plugs for everyone on the driving range and golf course. The Area 51 was loud; much too loud . . . and subsequently succumbed to a quiet death.
Fate: Dud

Brand: Wilson
Model: Staff Reflex Irons
Material/Mfg: Investment Cast 431 Stainless Steel with Urethane Channel Inserts
Back in the late 1970’s Wilson Sporting Goods introduced an iron with a thin face that trampolined the ball great distances. It was called the Reflex due to the spring-like nature of its face. Just like with a trampoline, a center impact would travel significantly farther than an off-center hit. Besides, the Reflex iron faces had a tendency to dent. I advanced the concept of the technology using an unsupported face with extremely thin variable geometry to it. This was coupled by placing expansion joints in the sole and toe of the design. The coefficient of restitution of the Staff Reflex irons measured higher than any other iron we could find on the market at that time. Since Fat Shaft’s were the shafts of choice during this project the Staff Reflex iron incorporated their use too. But Deep Red woods and irons began taking a strong hold of the Wilson product line during the Reflex’s development and R&D energies were redirected to other Deep Red projects. Hating to see a great concept die I utilized similar design technologies in the Golfsmith HiCOR irons that were introduced in 2006. In 2012 TaylorMade presented this concept into their own product line under the RocketBlades family.
Fate: Doomed
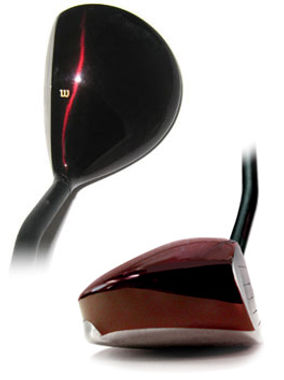
Brand: Wilson
Model: Deep Red Bi-Axis Drivers
Material/Mfg: Investment Cast 6-4 Titanium
I developed the Bi-Axis hybrids for Wilson Japan while co-developing the Deep Red Bi-Axis driver for the U.S. market. This design incorporated a curved shaft tip that helped stabilize the head on off-center impacts. Using a second shaft axis to stabilize impacts has been applied on double bend putter shafts but this was a new concept for non-putters. In addition to the woods I also developed a Bi-Axis iron which also incorporated the curved tip shaft. Varying degrees of offset could be used for a single head based on the amount of tip trimming applied to the shaft. In addition, varying the tip trimming also provided different loft and lie specifications without making adjustments to the head. One of the biggest challenges with the Bi-Axis program was the bladder molded shaft production. Maintaining tight tolerances on the shaft-over-hosel composite design became an issue with the Wilson Japan production. Subsequently Wilson's U.S. division chose to avoid taking a similar path with this model.
Fate: Doomed
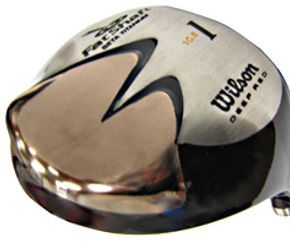
Brand: Wilson
Model: Deep Red Copper Sole
Material/Mfg: Investment Cast 6-4 Titanium with Copper Sole
As the Deep Red drivers expanded in size from their original 305cc design to over 400cc’s I also explored enhancements to the low/rearward center of gravity that drove the geometry of the driver’s design. Geometry is more influential than mass for driving the center of gravity to a desired location. With this concept I also increased mass density through the flame spray application of a copper-tungsten. The material was applied to the rear weight mass of the Deep Red’s sole and not only provided enhanced functionality through a higher MOI, but the cosmetic appearance of the copper-tungsten was a rich looking augmentation to the Deep Red translucent die coat.
Fate: Doomed

Brand: Wilson
Model: Deep Red “Bengal”
Material/Mfg: Investment Cast 6-4 Titanium
The concept behind the Deep Red translucent die coat was a new cosmetic innovation that influenced many other graphic finishes for driver and woods in years to come. I had spent a good amount of time perfecting the final die coat appearance and was challenged by Wilson’s marketing staff to come up with another unique cosmetic presentation following the driver’s success. Continuing with the die coat finish I introduced a number of different opaque finishes to supplement the translucent paint. One that I liked in particular (but not a favorite of the marketing group) was the Bengal striped crown. The black opaque paint was laid down on the raw titanium and the die coat was applied over the top. This provided a subtle effect to the presentation of the stripes. Subsequent generations took a more conservative approach to the die coat finishes.
Fate: Doomed

Brand: Founders Club
Model: Judge Strong
Material/Mfg: 17-4 Stainless Steel with Aluminum Oxide Face Insert
This Founders Club prototype was developed prior to the industry transitioning to titanium drivers. I had been exploring the use of different ceramic inserts in woods and wedges. This project followed the development of the Founders Club Dart wedges which utilized a pure ceramic insert of silicon nitride. Due to the difficulty of forming the bulge and roll necessary for a driver with silicon nitride the tooling for an aluminum oxide insert was created. The result was a good feeling and sounding driver but ultimately no performance benefits. Subsequently I played with the driver for a few years but the product never went to market.
Fate: Dud

Brand: Snake Eyes
Model: PowerLink Driving Irons
Material/Mfg: Investment Cast 17-4 Stainless Steel with Carbon Fiber Body Insert
No matter how thin you can produce an iron face in stainless steel it will still fatigue or fail over a short period of time. 17-4 stainless steel was used for the PowerLink driving irons due to the higher strength properties compared to 431 stainless steel. But a 0.85mm face cannot survive without the reinforcement of a strong material behind it, hence the light weight molded carbon fiber insert that fit into the body behind it. There were a number of challenges with this design which included casting a consistently thin flat face, adhesion of the carbon fiber support and eventual durability over time from repetitive robot and air canon impacts.
Fate: Dud