Billet Forging
Billet forging golf club heads encompasses many steps to get to the completed design. The force behind the manufacturing process is the forging operation. Not all forging presses are rated the same. The presses shown below represent both ends of the forging spectrum. The 1-ton press on the left is primarily used for stamping and pressing. It works with sheet metal and does not transform a billet into a shape. Considerably more force is required to transform steel and titanium. The 800-ton press in the center is used for billet forging irons. The process shown on this page uses forging presses in this category rating. To the far right is the largest forging press in the eastern hemisphere. It is rated at 5,000-tons of force and is used to forge variable thickness beta titanium cup faces for drivers.

Billet Forging Irons

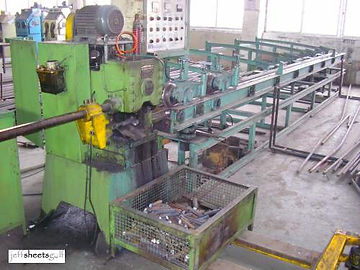

The iron forging process begins with the raw material. Here are rods of carbon steel approximately 25' in length. The carbon steel is sorted by its material properties and pulled from this inventory to create the billets used in the forging process.
A rod is fed into the cutting machine below and cut into per-designated lengths for the forging billets.

The billets are sorted and inventoried in anticipation of a manufacturing run.

From this point forward the operators on the forging team must work in orchestrated timing to runs the parts through the various forging presses efficiently. The first operator grabs the heated billets and feeds them to a press operator who forms a curve into the billet so that it can be fed into the first forging die.
The production run begins by taking the appropriate billet and running it through an furnace to bring the material temperature up to 2,400 degrees (Fahrenheit). For efficiency a conveyor runs through the billets up to fire forging temperature by the time they exit the furnace.


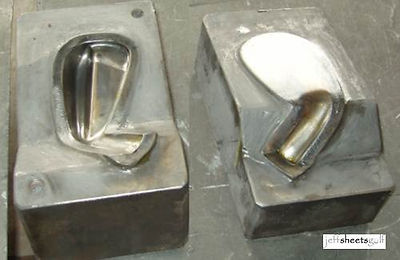
The 800-ton forging press will form the billet into the initial shape of the selected iron design. There are unique forging dies (tooling) that are committed to the iron design. The dies are manufactured from tempered steel to withstand the 800-ton force of the press.
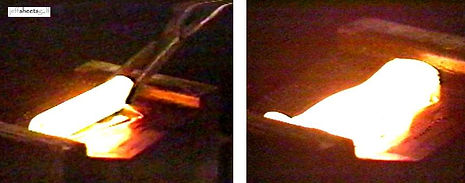



The heads will be fired up through the furnace once again to undergo the second forging press. This will compact the steel into a denser mass and provide more defined shaping to the iron head.
The newly formed part is fed into another press that removes the flashing - excess material around the profile of the iron face. With the flashing removed there is a part that has some resemblance to an iron head.

At this stage the heads will cool down before moving onto the next forging operation.
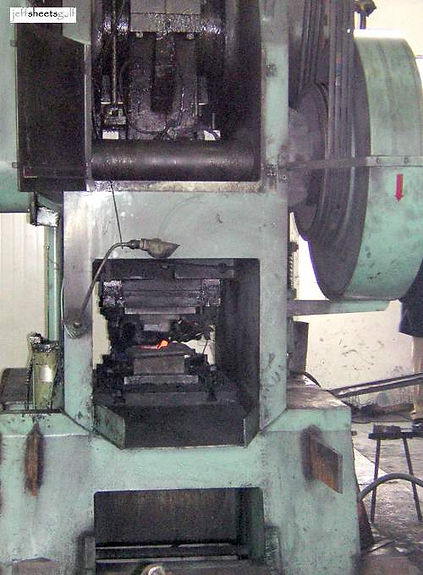
While still red hot the head will have the flashing trimmed off once again to remove excess material quickly and efficiently.



While the iron geometry is now taking on a define shape it is still very heavy with much more mass to it than the final spec calls for. Depending on the factory, a third and possibly a fourth forging process will compact the steel into a denser mass, squeezing out flash and lowering its weight.
Feeding heads into the furnace for the third forging operation.

Raw forgings, referred to by the factories as "AF" (as forged) ready for forging post operations.
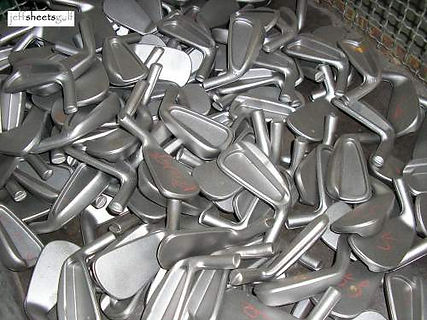

AF undergoing the coining process. Coining the head provides fine definition to the smallest details of the design. Some factories will forgo the coining operation while others may conduct multiple coining operations for a specific design.
Once coined the AF will go through numerous processes that no longer involve forging. One of the first post operations is boring the hosels. The system to the right works on a turntable that automatically bores the hosel to the blueprint specification.

Some iron designs call for a cast body and a billet forged face. Below are carbon steel forged faces that have also had CNC milling work done to the rear side of the faces.


Below the carbon steel forged face is plasma welded to its body. This is an automated process that limits the heat exposure to the head while minimizing the addition of weight that a welding rod would traditionally contribute to a design.

Plasma welded iron ready for normalization (heat treatment). The face will be skim milled flat before score lines will be added.


Another design approach used with the forging process is the CNC mill the cavity of the head. A "generic" blade design is forged that incorporates specific design parameters involving offset, blade length and sole width. By CNC milling the back of the heads a generic forging die can be used to produce an infinite number of iron designs.
At this stage the iron is ready to have the face milled flat and score lines engraved.

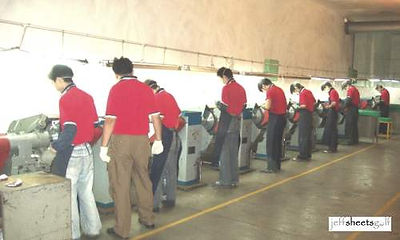
Head polishing will follow by shaping the iron to its blueprint specifications and hitting the appropriate target weight. This operation can yield various results based on the individual polisher so these personnel have the most experienced eyes in the manufacturing operation.
Heads fully polished and ready for specification inspection.
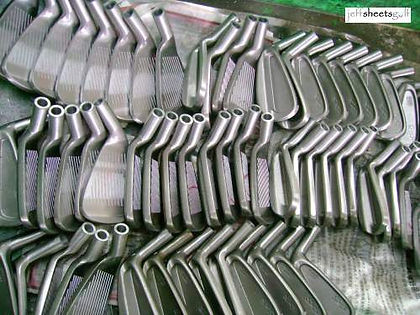

After loft and lie specifications have been adjusted the heads are ready for face and cavity prep. Faces will be glass bead blasted along with the cavities. The rest of the iron head must be protected from the blasting media with protective tape.


Once the iron heads have completed the polishing and cosmetic surface prep they are ready for chrome plating. Carbon steel oxidizes and rusts quickly so the plating process is necessary to retain the polished finish.
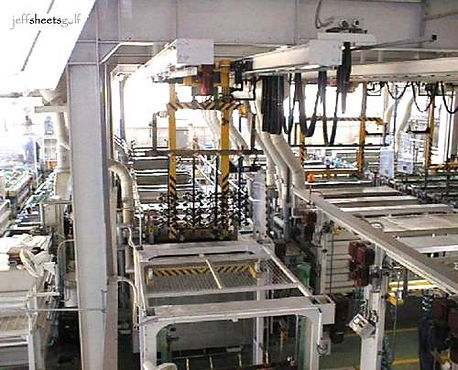

The finished part! Many hands have touched each head by the time they are ready to be shafted. The final product should be a jewelry-like product that represents a compliment of art, engineering and manufacturing.
From Billet to Iron Head
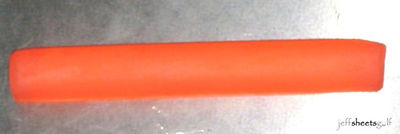
The billet is heated to 2,400 degrees Fahrenheit making the carbon steel more pliable.

1st Forging - The billet is formed into the general shape of an iron.
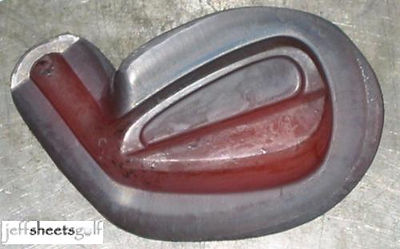
3rd Forging - Details of geometry are increase as compaction of steel becomes greater. More flash is generated as the material is squeezed tighter together.
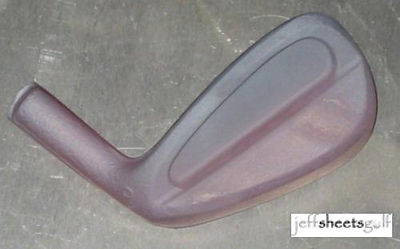
4th Forging - 1st of the Precision Presses also referred to as Coining. Imparts more refined detail and finer surfaces.

Completed raw forging - also known as AF (as forged).
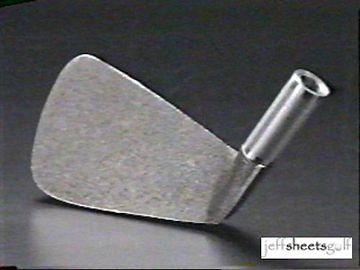
Hosel is bored to the appropriate I.D. (inner dimension).

Scorelines are applied to the face and then the head undergoes hand polishing to final specification.

The billet is bent prior to its insertion into the forging die so that it better conforms to the die geometry.
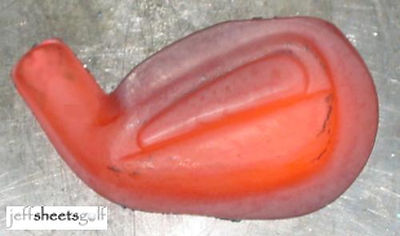
2nd Forging - Greater detail is imparted into the design as the second die compacts a refined geometry to the iron head. The flash (excess material surrounding the face profile) is removed by a special forging die.
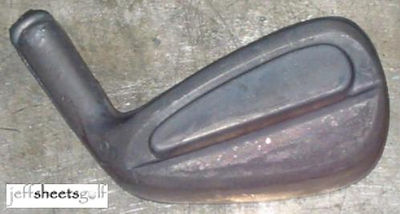
Flash trimmed off after third forging.

5th Forging - 2nd of the Precision Coining.

Hosel is machined to the blueprint O.D. (outer dimension).
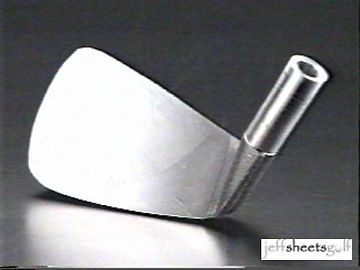
The face is planed flat.
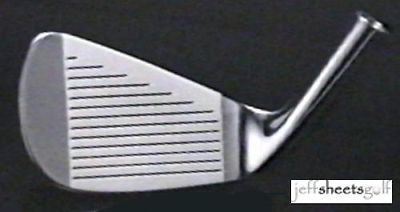
Head is chrome plated and ready to ship to customer.